Workforce training program created for Richmond biomanufacturing plant
Subscriber Benefit
As a subscriber you can listen to articles at work, in the car, or while you work out. Subscribe Now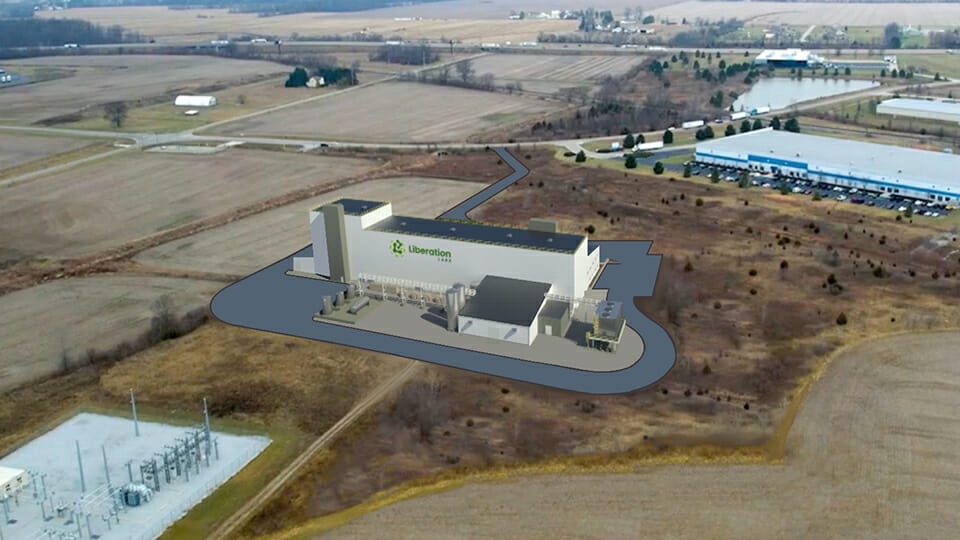
New York-based Liberation Labs is partnering with Ivy Tech Community College in Richmond to train future employees at the company’s $115 million biomanufacturing facility currently under construction.
The biomanufacturing workforce training program, the company said, will equip the workers with the required skills to work in precision fermentation, which is the primary focus of the facility.
Liberation Labs says the goal is to ensure that about 30 people are trained and ready to work in the plant when operations begin later this year.
CEO Mark Warner told Inside INdiana Business the company is focused on hiring local people, which provides a wide range of work experience.
“Probably half our positions only require a high school degree. Yet, my personal experience is we may get people with bachelor’s degrees applying,” said Warner. “So, you have to bring all those people up to the same level of experience, both industrially and with the modern biotechnology.”
Plans for the facility, located at Richmond’s Midwest Industrial Park, were first announced a year ago, and construction began in June.
The plant will produce alternative proteins, which are used in food products such as almond milk and plant-based meat, as well as agricultural products such as biopesticides, with a fermentation capacity of 600,000 liters.
Liberation Labs says training program will include classroom, laboratory and online training. An on-site training component will be added later. The curriculum will cover biotechnology fundamentals, fermentation fundamentals, biomanufacturing best practices, quality, compliance, and health & safety.
Warner said the specific education on biomanufacturing will be critical for the workers beyond just the general industrial knowledge that will also come with the program.
“We need employees being more than just, as an old boss of mine used to call them, widgets doing what they’re told, but understanding the process,” he said. “I can tell you from personal experience having managed plants, you get the right shop floor people, you’re going to get way more productivity out of your facility, but they have to understand the core process and why they’re doing what they’re doing.”
Chad Bolser, chancellor of the Ivy Tech Richmond campus, says the development of the program has been exciting because the biotech space is a new for the region. He said the campus has been able to draw upon the college’s statewide expertise to develop the training.
“Biotech is new for our campus, but not new in Ivy Tech Community College,” he said. “There are programs in Indy and Bloomington and lots of areas that we can draw expertise on. That development process takes place through our skills training and our workforce development operation, along with our faculty, in this case, from other campuses, and integrated with the obvious expertise of Liberation Labs.”
Liberation Labs expects to begin hiring in this spring, with the training commencing ahead of bringing the workers on-site in late summer.
Warner said he is very confident that the company will be able to find the workforce it needs for the plant. The initial plan is to hire a total of 45 people, about 30 to 35 of whom would be hourly, but the company eventually plans to expand the facility and bring its headcount to around 150.
While the training program is specific to the Liberation Labs operation, Bolser said the framework of the partnership between the two is one that could be replicated in the future and used as a business attraction tool.
“What it allows for us is to do what Ivy Tech does best, which is to develop customized training, to meet the needs on-demand of employers, and to do it in a way that meets current needs, but also future needs,” he said. “We’re just excited that this sector is coming into our area, and we can be in the ground floor of it.”