The new workforce equation: Navigating staffing in manufacturing
Subscriber Benefit
As a subscriber you can listen to articles at work, in the car, or while you work out. Subscribe Now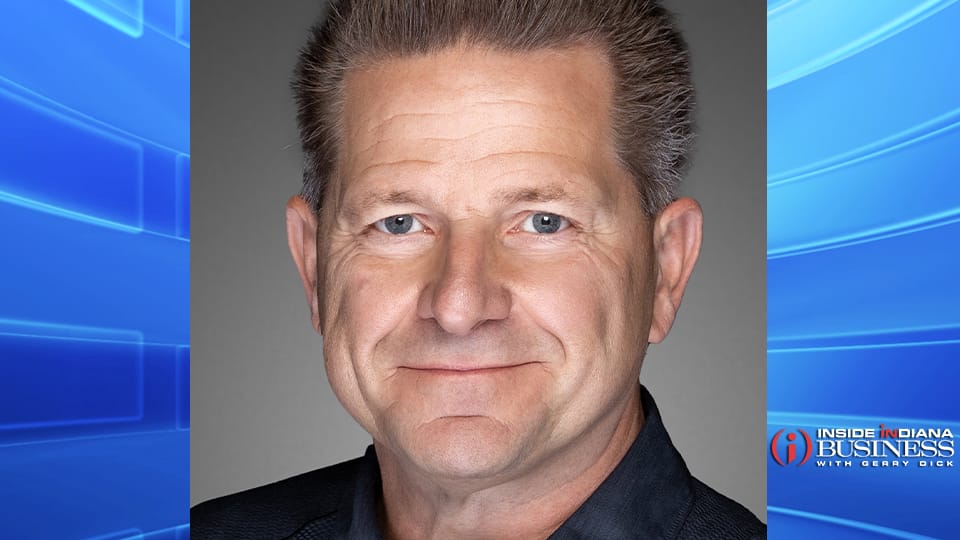
Manufacturers today face an intensifying risk profile driven by complexity, speed, and unpredictability. Workforce challenges have evolved beyond conventional solutions, and now pose greater threats to operational stability and competitiveness.
If your workforce strategies aren’t keeping pace with the demands of modern manufacturing, the solution isn’t in choosing between AI, workforce optimization, or staffing—it’s in combining them.
AI vs. Automation: Understanding the Difference
Before we explore the power of this integrated approach, it’s important to clarify the roles of AI and automation:
- Automation executes repetitive, rule-based tasks with reliability but lacks adaptability. For example, an automated assembly line halts if materials are delayed, with no capacity to adjust dynamically.
- AI, by contrast, learns and adapts. It uses data to make real-time decisions, detecting patterns, anticipating disruptions, and adjusting processes dynamically. AI might forecast workforce needs based on production schedules or real-time demand, enabling manufacturers to pivot before problems escalate.
Automation excels at execution, while AI brings intelligence. Together, they create a system capable of both reliability and flexibility.
The Power of Integration: AI, Workforce Optimization, and Staffing
The future of workforce strategy lies in combining AI, workforce optimization, and staffing into a cohesive system. This integration isn’t just additive—it’s transformative, multiplying the strengths of each component:
1. AI as the Catalyst
- AI powers predictive capabilities such as forecasting labor needs, identifying skill gaps, and dynamically reallocating resources in response to disruptions. It’s the brain behind smarter workforce decisions.
2. Workforce Optimization as the Framework
- Optimization provides the structure for aligning human and machine resources with operational goals. It transforms AI insights into actionable strategies—whether for scheduling, task distribution, or long-term labor planning.
3. Staffing as the Execution Arm
- The best strategies still require execution. Strategic staffing ensures manufacturers fill roles with the right talent, at the right time, and with an eye toward adaptability and retention.
How It Works in Practice
Consider a manufacturer facing unpredictable customer demand and supply chain volatility. Here’s how integration can deliver results:
- AI Predicts Workforce Needs: AI analyzes production data and external variables to anticipate a 20% production increase next quarter.
- Optimization Aligns Resources: Workforce optimization adjusts staffing plans, identifies shifts requiring more coverage, and proposes cross-training opportunities to address gaps.
- Staffing Executes the Plan: Recruiting focuses on adaptable candidates, while current employees are scheduled efficiently to balance workloads and prevent burnout.
This integrated approach doesn’t just react to problems—it anticipates and solves them, creating resilience in the face of uncertainty.
Overcoming Barriers to AI Adoption
Some manufacturers hesitate to embrace AI due to misconceptions about complexity or cost. The reality is that AI solutions tailored for workforce challenges are both accessible and practical:
- Misconceptions About Cost: AI tools for workforce scheduling and labor forecasting often deliver immediate savings by reducing overtime, absenteeism, and inefficiencies.
- Building Trust in AI: AI doesn’t replace human decision-making—it enhances it. By taking over repetitive tasks, it frees managers and employees to focus on higher-value activities.
- Starting Small: Pilot projects, such as predictive scheduling or absenteeism management, offer low-risk opportunities to see measurable results quickly.
Identifying Your Workforce Challenges
To begin this transformation, manufacturers must first understand where inefficiencies lie. Common challenges include:
- Absenteeism and turnover disrupting production.
- Reactive scheduling driving up overtime costs.
- Skills gaps that slow productivity and innovation.
Adding to these challenges, potential policy changes—such as stricter immigration enforcement—could disrupt labor availability, further underscoring the need for resilient, proactive strategies.
Strategic Partnerships Make the Difference
Even the best technologies require the right expertise to implement effectively. Partnering with an unbiased subject matter expert ensures AI tools are aligned with your workforce goals and delivers measurable results.
Conclusion: The Competitive Imperative
Traditional workforce management methods are becoming increasingly ineffective, and demand an innovative, integrated approach. The question isn’t whether you can afford to adopt it; it’s whether you can afford not to.
Kent Burns is the Founder and CEO of Simply Driven Workforce Solutions and Simply Driven Executive Search. He has over 25 years of experience in the recruiting and staffing industry.