Q&A with Jerry Roach at Kimball International
Subscriber Benefit
As a subscriber you can listen to articles at work, in the car, or while you work out. Subscribe Now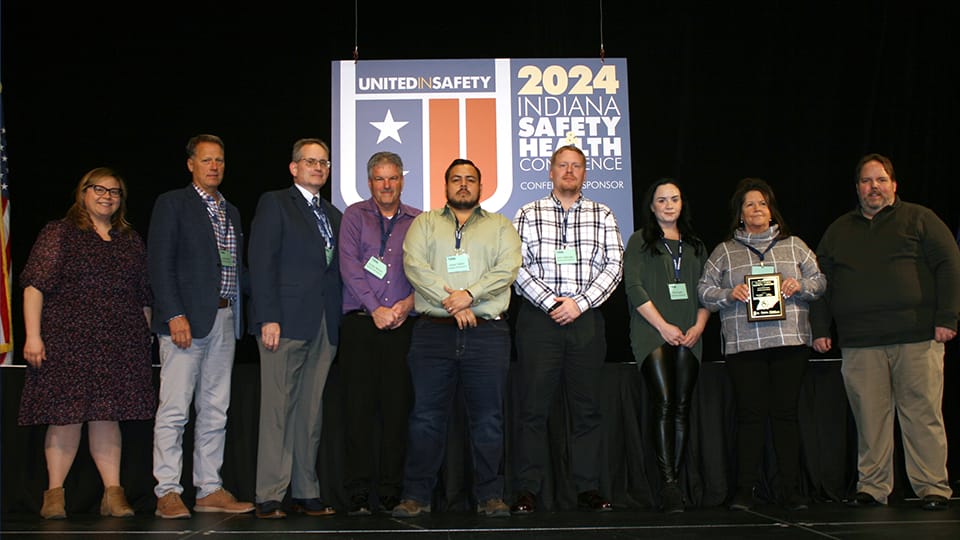
Jasper-based Kimball International was recognized with a 2024 Governor’s Workplace Safety Award for education and outreach at a ceremony in Indianapolis last month. Jasper-based MasterBrand Cabinets also won an award from the Indiana Department of Labor for innovations at its Ferdinand plant.
Kimball opened its employee health center in 2019 and recently added a physical therapist to its ranks to assist employees with health issues that arise.
Jerry Roach, corporate safety and environmental director at Kimball International, spoke with Inside INdiana Business about workplace safety challenges and Kimball International Health Clinic’s newest addition.
How was Kimball International nominated for a 2024 Governor’s Workplace Award?
The safety professionals, every year they put it together, and then companies have an opportunity to nominate the work that they’ve done. In December, early January, you start receiving emails saying the nominations are going to open on this day.
It comes down to, what have we done that would even get us in a position to deserve such an award? And then actually filling out the documentation, which isn’t easy. You have to make sure you pinpoint everything, and, thankfully, we’re pretty good about having all of our documentation and data to back everything up. And then you send it in.
I was told they received a bunch of nominations this year, and it wasn’t easy deciding who was going to receive the awards, but that our team members, when it came down to it, stood out with what they were able to accomplish in 2023, going into 2024.
How does it feel to win this award for education and outreach?
I was thrilled. This is the fourth time I’ve been on a team that has won this award. At Paley Furniture, which was in Orleans, it’s no longer in business, we won it twice. And then Kimball Electronics and now Kimball International. When you get that phone call or receive that email, you know that it’s not happenstance that you received it. You know that it was a total team effort and that it’s for everybody.
It took every single person within the company to make that happen and reach those goals so you could even apply. Because if everybody’s not doing their jobs correctly and making safety the top priority, then everything is so backward it wouldn’t make sense to apply. So, it felt fantastic. It really did.
For us, it’s not just safety first. It’s safety first, last and always.
Tell me about the health clinic, the early intervention program and adding a physical therapist last year.
When you walk in, you’re not just walking into a health clinic. It’s also showcasing all of our health care furniture.
We’ve had the early intervention program at Kimball International for a long time. I can go in today—and it doesn’t matter if I did it at home or if I did it at work or if I’m not even sure—and my elbow is bothering me, what are we going to do about my elbow? How about we jump on that and get our physical therapist involved and see what can we do to help you?
What are some stretches? What are some exercises? Maybe it’s the way I’m doing my job a lot of times. We do a lot of ergonomic work, all of our safety teams do. And we involve our physical therapist a lot. Because maybe it’s a movement that I’m making that I don’t even realize I’m making. That happens a lot. And not only in our production facilities but in our offices, too. Maybe it’s the way I’m sitting. Maybe it’s the way I’m not standing at all during the day.
We try to get in there quickly and to assist them. The early intervention program helps individuals not only today but down the road. A lot of times, especially with ergonomic situations, you’re not taking care of the injury today as much as you are the long-term injury that somebody could have of doing the job over and over. You’re saving them from that body ache 10 years from now.
How have employees responded to the new physical therapist?
It’s been almost overwhelming to see the reaction and the participation and the physical therapist walk through a plant and individuals stopping them and saying, “Hey, this happened at home last week. I need some help.” And he’s right there to help them in any way possible.
Maybe they would have a pinched nerve or something. He can’t fix that, but he can help them move to the next step because it isn’t something physical therapy can fix. But he can help them understand that.
He does a lot of education. It’s gone over way beyond what I thought it would. It’s been amazing to watch and to be a part of it.
What are the challenges of enhancing workplace safety?
One is helping people think about safety because nobody gets up in the morning and says, “I’m going to work, and I’m going to get injured.” But guess what? There are going to be injuries today, unfortunately, throughout the industry. Fourteen people in American industry are going to get killed today. That’s horrible to even think about, but that’s going to happen. So how do we help individuals and teams think about safety?
We talk about safety at the start of every shift, every single day. We also do stretching, which is part of our early intervention program. We have stretches that are for the particular job that I would be doing. We want to get the body warmed up and the blood flowing, but what we’re really doing is getting the mind to think differently.
The departments do stretches at least twice a day. Once after lunch and then once at the beginning of the shift. Because once you come back from lunch, you ate too much or you were listening to music or having a discussion with somebody, and your mindset is not there. We’ve got to get our mindset on safety again and then finish up the day.
A lot of companies are like, “We’ve got to get this out the door. We’ve got to get this product on the truck.” Well, if it puts somebody in danger of getting injured, that product doesn’t matter as much as that person. We always have to remember that the person, the individual, the team member, they matter much more than anything we possibly could make. We cannot put our teams in hazardous situations.
One of the things that we talk about with our team leaders all the time is to go to your team or go to an individual and ask, “What at work today could injure you?” I’ve never had anybody say, “There’s not a thing here.” Whatever that answer is, okay, let’s fix it. Let’s correct that issue. We also do proactive safety improvements. We have to be looking for hazards all the time, and hazards change.
If you have 150 or 250 people working at a plant, that’s a lot of people to see hazards and to get those taken care of. There are times you can’t fix things overnight. But what can we put something into place that will keep somebody from getting injured until we can fix it? We may have to order parts, which was difficult during the pandemic, but it’s gotten much better. We can’t leave a hazard and let it exist.
What’s the state of workplace safety?
For some companies, unfortunately, safety first is a sign at the door. Once you get past the sign, you never hear anything about safety again. Don’t get me wrong, there are a lot of companies throughout the state of Indiana and across the nation, who care about their employees and are doing the right things. But there are still several who are not stepping up the way they should.
They think it’s going to cost way too much money, which is sad because the truth is they’re still going to spend all that money. They’re just going to spend it on doctor bills. On the other end, they’re also missing out on building the pride and morale of the workforce. I see more and more companies trying to do the right thing but hesitant at times and maybe not sure what to do.
You’ve got companies who are trying to become compliant and barely reach that. And for a lot of companies, they’re like, “Okay, we’ve become OSHA compliant because we’re meeting all those standards. That means all of our injuries are going to go away.” You can be in compliance and still have a ton of injuries. People get injured in situations where standards are in compliance. So going above and beyond that is so important.
What’s the future of workplace safety?
It’s going to be interesting as we see more and more automation come to life. We’re doing that in our facilities, and a lot of companies are doing that, but we’re going to start to see that doesn’t mean all the injuries go away because we have robots doing things. Hopefully not, but potentially you’re going to see injuries related to using joysticks, holding a control panel, things of that nature. Is that the right way to hold it? Is the grip too tight?
A lot of folks think robotics and automation are going to take people’s jobs, and they will do some jobs that maybe individuals don’t want to do. But we’re going to see a change in the way jobs are being done, and from a safety standpoint, that’s going to create new situations that we have to look at and deal with.
Continuous improvement is a huge part of what we do at Kimball International. There are going to be hazards we don’t even realize or even know about right now that are going to come into play in the future as the business changes from a production standpoint. But it doesn’t mean that working safely goes away. It means that we have to do things a little bit differently. It’s going to be very exciting to see the future of safety and the future of production overall.
Anything else you’d like to add?
Safety is not a department. Safety is the business. If you don’t have safety, you’re not going to have the other things kick in. Your efficiencies are going to be worse. Things don’t flow correctly unless you have a safe workplace. We’re not perfect by any stretch. Every single day we work to improve, but if we can get safety right, it lines everything else up to be correct, also.
Every single day, the goal is to work safely and send our team members home to their families at the end of every shift. They may be a little bit dirty. They may be tired. If they’re not tired, we may have an issue. They may not be working hard enough. I know I’m tired at the end of the day. But that’s our goal. And if we can do that, then it’s been a positive day, to say the least.