Q&A with Brice Grinstead, VP at MasterBrand Cabinets
Subscriber Benefit
As a subscriber you can listen to articles at work, in the car, or while you work out. Subscribe Now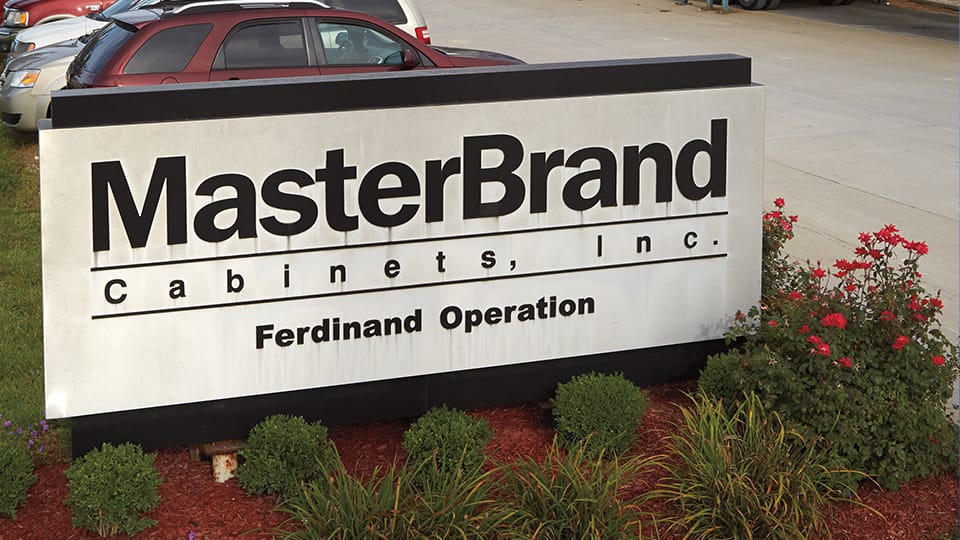
Last month, Jasper-based MasterBrand Cabinets won a 2024 Governor’s Workplace Safety Award for innovations at its Ferdinand plant. Jasper-based Kimball International was also recognized for education and outreach at the Indiana Department of Labor ceremony.
Brice Grinstead, MasterBrand’s vice president of environmental, health, safety and security, spoke with Inside Indiana Business about safety initiatives at the Ferdinand plant and the decision to move corporate headquarters to Ohio.
How was MasterBrand Cabinets nominated for a 2024 Governor’s Workplace Safety Award?
The Ferdinand team, the [environmental health and safety] leaders, drove that. They completed an application for the recognition. The application asked a number of questions about our safety program, how we measure our performance and our employee engagement.
And then those applications are reviewed by members of the American Society of Safety Engineers as well as the [Indiana] Department of Labor’s INSafe division. And then of those applications, that’s when we got selected for winning the award.
How does it feel to win this award for innovations?
The team’s really excited. The team puts in a lot of hard work, and they’re dedicated to what they do. And it’s a testament to what the Ferdinand team has done in the plant, and they’re proud.
Tell me about the Behavior-Based Safety program at the Ferdinand plant.
It’s one of the pillars of all of our safety programs. Ferdinand has been on that journey since about 2017, and they’ve been the one that’s shown the most success with the journey. That’s because it’s a grassroots program.
Many of the safety programs are rules and regulation-driven. The Behavior Based Safety program is about the employees owning the program. They audit themselves, they do peer-to-peer assessments and it allows them to drive the encouragement of safe behaviors in the plant as well as being able to coach unsafe behaviors. That’s led to some significant improvements in the plant.
How have employees responded to this program?
Employees love the program. It has been a huge success. We’re taking what we started in Ferdinand and using that across the rest of the organization.
The other thing that gets overlooked is that there’s an incentive to the program. The amount of auditing that they do, the plant allows them to have some of the plant’s funds. They use those funds to donate to local charities such as Ronald McDonald House and the YMCA. It drives community, culture, a sense of teamwork and belonging in the plant.
MasterBrand received the Governor’s Workplace Safety Rising Star Award in 2022, was named one of America’s Safest Companies by EHS Today in 2023 and received the Governor’s Workplace Safety Award in 2024. What contributes to these recognitions year after year?
I’ve been with the organization for 26 years, and it’s been a journey. We’ve grown in that time from about 2,000 employees to 13,000 today. It all starts with our employees living our safety culture every day.
Safety is part of our four basics. It’s woven into every aspect of our business. People often say safety is a priority, but we don’t view it as a priority. We view it as a core value of our business. It’s embedded in everything we do. We also have a robust safety management system, so it incorporates all the compliance efforts that we have but also allows us to look for areas of continuous improvement and ways that we can help the teams get better every day.
We have unwavering support from our executive team, our operations leadership. There’s never a question of what we’re going to do when we’re talking about safety in the plants. The last thing is that to get it to really work together, we’ve got to get 13,000 people all singing from the same songbook. And we’ve done a good job of getting to that point.
In what other ways does MasterBrand Cabinets enhance employee safety and health?
We have each of our plants do an annual safety plan, so they deep dive into the data and it tells them what they need to be working on moving forward to try to reduce injuries in the plant.
We also have something called Critical 15 that looks at the programs that could cause severe injury and have risks in our plants. Some examples would be lockout and machine guarding. We spend additional time, emphasis on those programs because they’re that important. We audit. We re-audit. We evaluate the plants. We talk about that all the time. We score ourselves. We reevaluate those programs to make sure that we’re not missing anything.
Ergonomics is another program that we spend a lot of time focusing on. That’s driven from our data that tells us that those are two programs that we need to continue to focus on to get better.
What’s the state of workplace safety?
Generally, we’re all in a very good spot. Obviously, COVID refocused all our efforts in that direction. My entire team was 100% focused on protecting our people during that time. But we’ve gotten back into the normal day-to-day stuff.
Workplace safety has come a long way since the adoption of the [Occupational Safety and Health Act] in 1970. That sets the foundation. It sets the rules and the regulations in the U.S. We have similar regulations for our plants in Canada and Mexico. But any ethical manufacturing organization is going to look for ways to go above and beyond what the rules and regulations say. And that’s what we do on a day-in and day-out basis.
What does the future of workplace safety look like?
What you’re starting to see is more automation, more use of robots in some of the manufacturing plants. And with that comes its own set of opportunities from a safety standpoint.
We’re looking at the automation aspect, specifically around our inspections and our data and how we can leverage that. Instead of filling out paper forms and tossing paper around, how we can use a streamlined system to help us with the audits and the inspections we have to do. It should be interesting.
The one aspect that I’m interested to learn more about is [artificial intelligence]. You’re going to see AI used in our industry to analyze data. To give us real-time data, to give us the insight to look at trends and tell us when we think things are going to happen in the future will just make us quicker and better at doing our jobs.
At the end of last year, MasterBrand announced the corporate headquarters move to Beachwood, Ohio. Why was that decision made, and what does it mean for the Jasper area?
Our spin from Fortune Brands drove us to establish a new corporate headquarters. Beechwood, Ohio was selected for several reasons, including the location in relation to our operations was still very centrally located as well as access to talent in areas that we didn’t have. We had to create our own legal group. We used Fortune Brands for all that before.
Our operations headquarters remains in Jasper. We’re committed to investing in that area. We have a large manufacturing presence in Dubois County, so we’re very committed to that area.
Anything else you’d like to add?
I’d be remiss if I didn’t take some time to thank the folks that serve as the catalyst as well as the conduit for all our continuous improvement on safety. And that’s our safety leadership across the organization. They have a very hard job, and sometimes it can be a thankless job, but they are the ones that drive the engine for us from a safety standpoint and make us successful today and will make us successful in the future.