Purdue Technology Turns Plastic Waste Into Fuel
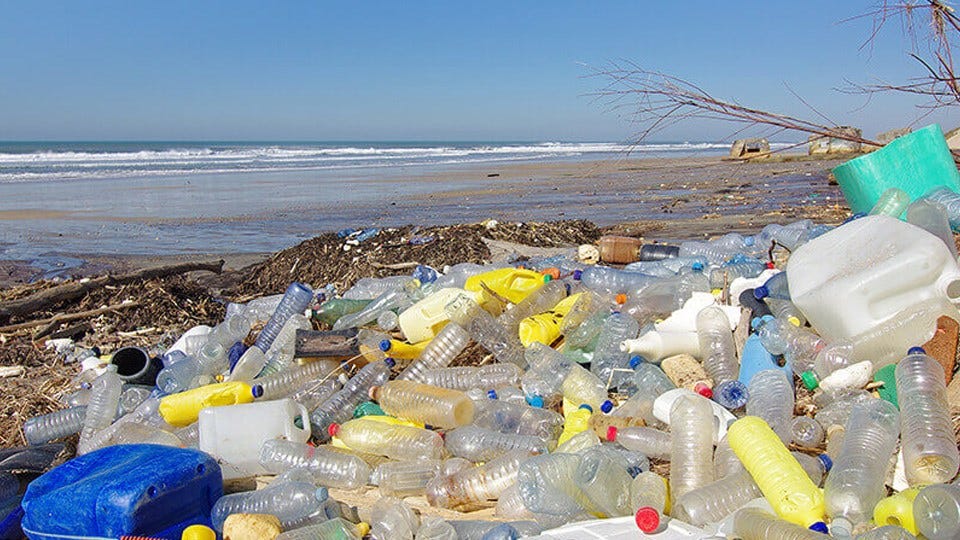
Subscriber Benefit
As a subscriber you can listen to articles at work, in the car, or while you work out. Subscribe NowWest Lafayette-based Hasler Ventures LLC is working to scale up a Purdue University patented technology that may accelerate the volume of waste plastic recycling. The innovation is called Low-Pressure Hydrothermal Processing. Hasler Ventures says the technique promises an economically viable and environmentally safe way to convert plastic into gasoline, diesel fuel.
In an interview with Inside INdiana Business, Chief Executive Officer Dan Hasler said the technology will be a viable way to recycle plastic into higher value products.
The technology was developed by Linda Wang, a professor in the Davidson School of Chemical Engineering, and the research was published in a 2021 issue of the peer-reviewed journal Fuel.
“Its basically a pressure cooker,” says Hasler. “The technology that Linda and Purdue have developed basically allows for a process that using less energy and a lower temperature with pressure allows you to be able to render this plastic down to its core elements using a lot less pressure.”
Hasler says the amount of pressure and heat required with previous technologies made the process economically unviable.
“The key to solving this problem is to make it economically more attractive to collect and process the plastic waste stream into higher-value products at a significantly lower conversion cost,” said Hasler. “Current methods including incineration, pyrolysis and mechanical recycling have all proven to be ineffective or too costly, both financially and environmentally. They have not been able to draw the required private investment at a scale sufficient to divert the vast majority of the global 350 million tons of plastic waste produced annually from the landfill.”
Hasler says the world is trying to recycle plastics, its just not doing it very efficiently.
“A very small percentage of plastics that are delivered to us actually gets recycled and reused,” he said. “A large amount of it simply gets recycled by melting it down and molding it into something else like a lawn chair or deck siding, etc. Which is fine and great, its just that the value-add, the economics associated with doing that, aren’t great enough to encourage mass collection of plastic for its purpose.”
According to Hasler, the first order of business is to demonstrate the technology outside of the laboratory and in commercial volumes.
“What were hoping to do is demonstrate that this process makes it worth someone’s while to not just accept plastic at their doorstep but actually go find it and pay people for their plastic because I can turn it into something much more valuable, thereby, keeping it out of the landfills and oceans,” said Hasler.
Hasler Ventures is collaborating with American Resources Corp. (Nasdaq: AREC) to use its Indiana-based chromatography pilot plant, currently in development, to demonstrate the technology.
Hasler says he hopes to be using the technology at commercial volumes in four to five years.
Hasler explains how the technology could be an economically viable solution to plastic waste recycling.