Purdue researchers design high-efficiency powertrain
Subscriber Benefit
As a subscriber you can listen to articles at work, in the car, or while you work out. Subscribe Now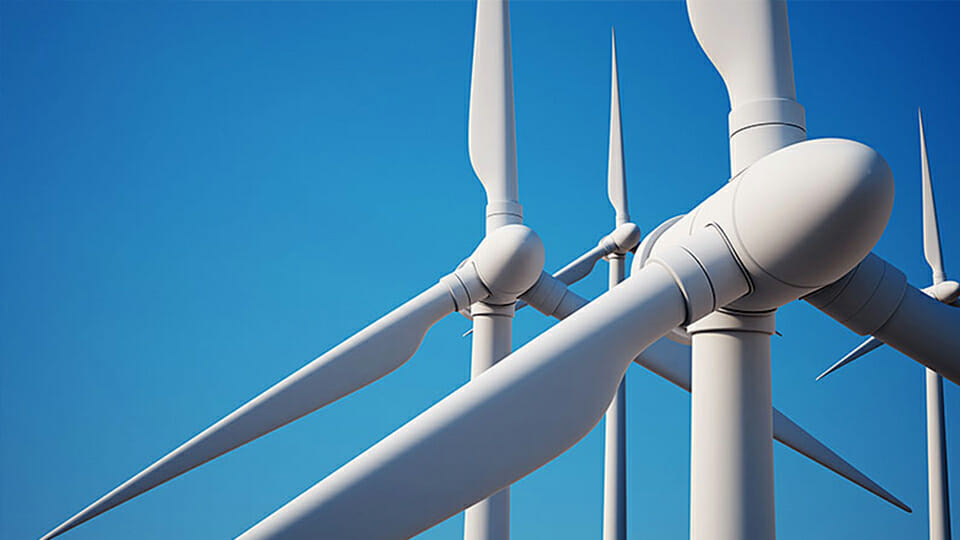
A pair of engineers at Purdue University are working to improve the efficiency of turbines used to generate wind and marine hydrokinetic energy. A low-speed, high-torque powertrain system has been designed to reduce operational and maintenance costs, as well as environmental contamination of turbines.
The powertrain system was designed by Jun Chen, a professor in Purdue’s School of Mechanical Engineering, and Lizhi Shang, an assistant professor in the Department of Agricultural and Biomedical Engineering and School of Mechanical Engineering.
A wind or hydrokinetic energy turbine requires a powertrain system to transmit energy from the turbine to a generator that will convert the energy into electricity.
Chen says a turbine typically features a high-torque, low-speed operation, but an electric generator prefers a constant high speed. However, a multi-stage gearbox is needed for the energy transmission, which causes the generator to run at variable speeds.
According to Purdue, Chen and Shang’s powertrain system is designed to transmit the power from the turbine to the generator while maintaining a constant generator speed. Shang says because of that, the generator can be moved to a more optimal location.
“That benefit can be, let’s say on the wind turbine, we can move the electric generator to the ground level. In the case of a hydro turbine, we can then also move the electric generator from under the water to surface level,” said Shang. “We also have the technology that is able to convert this very challenging low-speed, high-torque wind turbine power to the fluid power.”
Currently, the generators and gearboxes on wind turbines are located on a tower hundreds of meters above the ground and weigh hundreds of pounds. Moving them to the ground, Chen says, will reduce the weight of the turbines and simplify maintenance, resulting in lower costs for the operator.
Shang adds the design allows for smart, collective harvesting of energy using an array of individual turbines and one or more centralized generators.
“Turbines can be connected fluidly to their neighbor turbines,” said Shang. “A common, high-pressure fluid network can be established to connect all the turbines and generators of a collective turbine array. The network allows for strategically selective operation of the generator to keep some of the generators running at their most efficient points and shut down the rest to reserve lift time.”
Shang says the system also creates an environmental benefit by using water as the working fluid for the powertrain instead of hydraulic oil.
“The benefit includes higher efficiency because the stiffness of the water is higher than [oil],” he said. “It’s environmentally friendly. If we have any potential leakage of the working fluid due to the pump motor connection…it won’t really damage the surrounding environment. Plus, if we’re talking about a hydro turbine, then we can also protect the hydraulic system itself.”
Chen says using water instead of hydraulic oil in their new powertrain system is up to 90% more efficient than current systems.
Purdue says the next step in the powertrain’s development is to test a prototype in a towing tank on the West Lafayette campus. The researchers will collect, measure and analyze data in order to further improve the design.
“We want to put the prototype on top of another wind turbine,” said Chen. “We’re thinking of…those old turbines which are 20 years old that are at the end of their life duty. We’re working to get connected with then to install one of our units onto those systems and do a real on-set test.”
Chen and Shang are working with the Purdue Research Foundation Office of Technology Commercialization, which has applied for a patent on the design.