Project rescue 911: Business process reengineering
Subscriber Benefit
As a subscriber you can listen to articles at work, in the car, or while you work out. Subscribe Now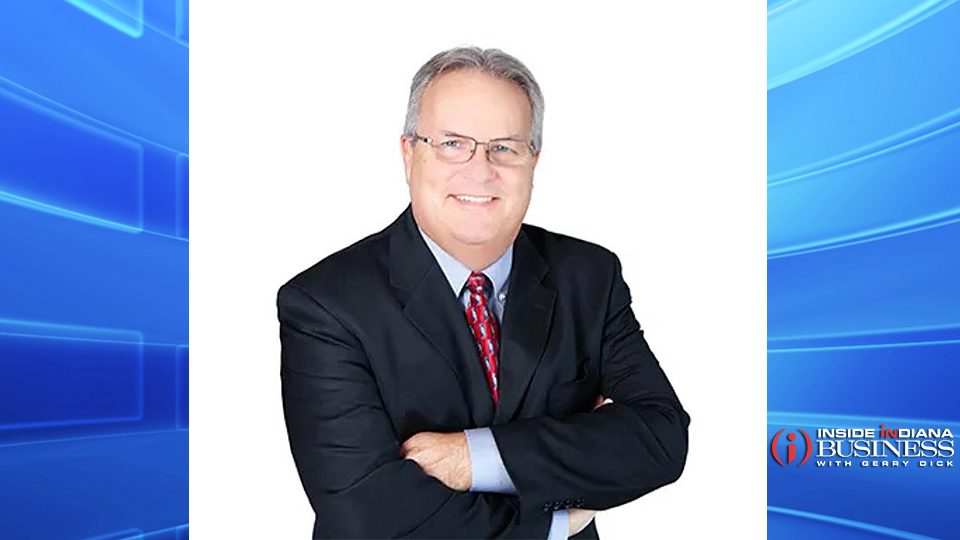
Technology can optimize your supply chain and logistics processes, but as with everything in business, there are always risks involved that can disrupt the flow due to circumstances that might be out of your control.
When those unexpected changes or breakdowns occur and throw your supply chain into chaos, there are some techniques you can tap into to get you back on the right path and move the process forward and allow for the continuation of critical business processes.
Troubleshooting
Supply chain management relies on business strategy, software and collaboration and each step in the process is dependent on the other. It is important to initially determine where the inefficiencies might lie in your current processes, from suppliers to manufacturers and beyond, why the process is being executed that way, what can be done to recreate a set of core business processes, and identifying and documenting any issues with the current processes that you may need to address.
You have to start at the beginning, documenting the as-is processes and the current state of the way in which the organization functions before you can define to-be processes and the optimal path forward to eliminate unnecessary and inefficient aspects of the workflow. By identifying the issues with current processes as well as documenting the opportunities for improvement you can properly identify the impacts of any disruption and begin to develop a plan to rectify. The goal is not to dwell on the missteps of the past, but to learn from them and create the most productive business result moving forward with a focus on reduced cost, increased output and increased quality.
Measuring the Tangible Along with the Intangibles
While capturing and collecting the data that is being created is key to the logistics process, you cannot always rely solely on data to tell the complete story. It’s the information that is hidden from view, the people involved, the undocumented tasks and hidden intermediate data sources utilized in the process as well as the different scenarios that an organization must also review and understand.
Having a roadmap helps determine who needs access to the data and when, if you have the right number of team members with the right skillset to handle the volume of data, and if you are on the same page with your customers as it relates to the way in which the data is shared. If you aren’t looking at the intangibles and aware of the factors outside of metrics that need to be factored into your decision-making, then you are missing a key opportunity to align your tactical measures and process design with your strategic direction to achieve your desired business results.
Think ahead, have a backup to your backup plan
We are always willing to help customers in need, but our preference is to support advanced planning versus the stress of changing or updating a process in the midst of a crisis. Always plan for the worst-case scenario. Take into consideration the current process model, issues and requirements, system capabilities and create a To Be Business Process Model for each of the known areas where a disruption may occur.
Lastly, don’t just let the reengineered model live in theory, test the implementation of your “plan B” so you can hit the ground running when your current system goes awry. Manage the risk and practice being uncomfortable with your team in order to adapt quickly to the possible change. The more they have run through the testing and determined the threats and alternative implementation methods, the more likely they are to learn something new and feel better prepared to handle the unexpected.
Security
Forward-thinking businesses must also adapt their security management planning in order to thrive. We live in a time when cyber attacks are becoming bigger, scarier, more sophisticated, and more frequent. Not pivoting your business processes and operations to account for this unrelenting uptick in ransomware and other cyber threats is no longer an option.
As you’re navigating a changing process, consider how securing your data could better serve you. It’s important to understand where your business currently falls in terms of strengths and shortcomings when talking about cybersecurity. Use those findings to incorporate an information management plan toimprove resilience against possible interruptions.
In 2022 alone, total e-commerce sales were estimated at $1,034.1 billion, an increase of 7.7% from 2021. Demand and interference due to the pandemic may have disrupted many traditional supply chain and logistic models. Reengineering the process to address changes improves efficiency and can reduce cost, increase output, increase quality, and ultimately give your organization a greater competitive advantage.