Funds to Focus on Work Force in Manufacturing Hotbeds
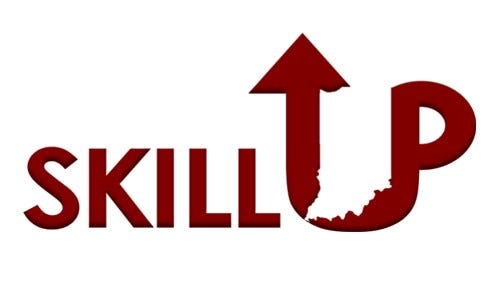
Subscriber Benefit
As a subscriber you can listen to articles at work, in the car, or while you work out. Subscribe NowAlthough in opposite corners of the state, two Indiana regions share an identical challenge: the struggle to find workers to support area manufacturers. Northwest and southeast Indiana are two manufacturing hotbeds, yet work force leaders say employers struggle to fill current openings and voice concern about the pipeline of tomorrow’s workers. The regions are among many in the state to earn a slice of an $11 million pie aimed to train Hoosiers with skills tailored to their specific region.
“Manufacturing represents close to 40 percent of the employment base in [southeast Indiana],” says Community Education Coalition Executive Director Kathy Oren. “We’re hearing about strong challenges in filling skilled labor, and a lot of that is middle skills: precision machining, computer-aided design (CAD), electronics and welding.”
EcO Network of Southeast Indiana, a 10-county education, business and government collaboration, is one of 13 recipients in the state to be awarded a SkillUP Indiana! grant to create or adapt training programs to match local employers’ needs. The Ohio River Bridges Project—to be complete in October—and the River Ridge Commerce Center in Jeffersonville are expected to drive development in the area and attract even more manufacturing to the region.
“Not enough students are getting involved in career technical education while in high school, and clearly, not enough students are coming to Ivy Tech [Community College] to gain those types of skills,” says Oren. “The automation and robotics program at Ivy Tech is an excellent program; students can take classes, work at Cummins, Toyota, Honda or other local manufacturers while they’re getting a two-year associate degree and be hired immediately. Just not enough seats are filled in those types of programs.”
EcO is using $1.8 million from the SkillUP initiative to create 17 projects to increase the number of high school and higher education students and adults gaining the job skills local industry demands. Advanced manufacturing is a major focus, and one such project is the Cub Manufacturing program. Already in place at one local high school, it helps students develop and build a product needed by a manufacturer in the area.
“This bubbled up as a way to get more students involved and interested in manufacturing as a career,” says Oren. “We’ll be expanding Cub Manufacturing through the SkillUP grant to Batesville and Seymour.”
In the opposite corner of the state, the Northwest Indiana Manufacturing Consortium is using about $428,000 to close its regional skills gap. Center of Workforce Innovation President Linda Woloshansky says manufacturers there are also hungry for middle skill workers to fill vacant positions.
“About 33 percent of our gross regional product (GRP) comes from manufacturing,” says Woloshansky, “which is actually higher than the state’s GRP in manufacturing; it’s extremely concentrated here.”
Woloshansky says that requires an extremely concentrated work force to match.
“We have a lot of people in manufacturing who need to upgrade their skills to keep up with the ever-changing industry, which is fueled by new technology that’s requiring a lot of changes in skillset,” says Woloshansky. “In the past, we’ve had these fragmented conversations—one-on-one where a school talks to an employer—and it never gets the traction it needs to make sure all the training is lining up.”
Woloshansky says the consortium, which includes 22 manufacturers in the region, has identified “the common denominators”—the training areas employers find most important. In addition to tweaking existing programs and adding new ones, the region will have a 20-hour Manufacturing Bootcamp for residents to learn about the industry and what training is needed.
With programs backed by dollars and collaborations led by industry, northwest and southeast Indiana are hopeful the increased focus on training will help fan the flame of manufacturing in their respective regions.
Oren says manufacturing employers working with career and technical education directors “can really make a difference.”
Woloshansky says the Northwest Indiana Manufacturing Consortium identified the mechanical electric area as one in which workers are lacking updated skills.