Evansville manufacturing roadmap reveals industry status, growth plan
Subscriber Benefit
As a subscriber you can listen to articles at work, in the car, or while you work out. Subscribe Now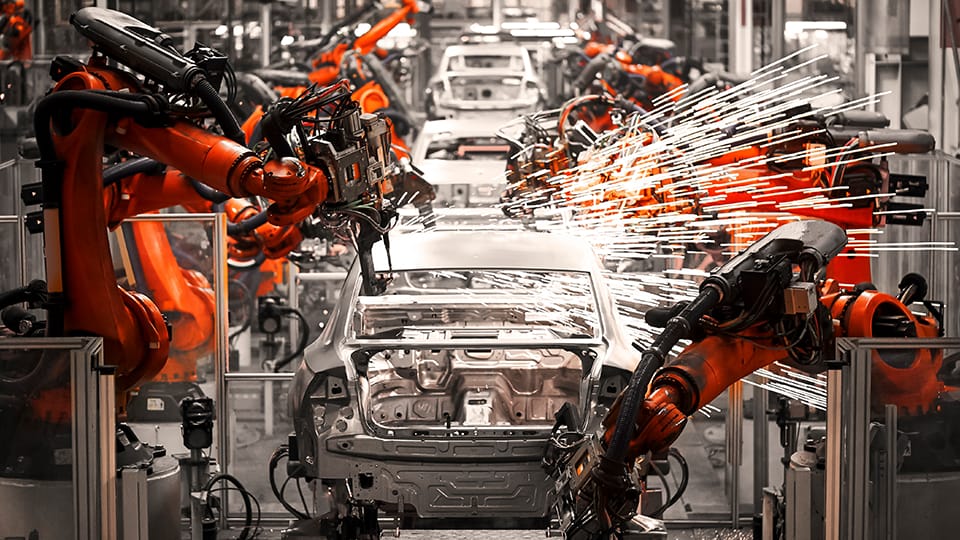
Last month, the Evansville Regional Economic Partnership and the Tri-State Manufacturers’ Alliance presented the Evansville Regional Strategic Manufacturing Roadmap. The report analyzed the state of regional manufacturing and provided strategic recommendations to advance the southwestern Indiana sector.
Tyler Stock, executive director of Talent EVV at E-REP, said the roadmap’s objective is to combine assets already in the Evansville region with best practices of other manufacturing-intensive regions to help solidify future economic vitality.
“Each of [the recommendations] is either a national best practice or something that surfaced directly from our industry partners to say, ‘This is something we need, or this would be helpful for us to grow our business,’” he said.
More than 50 local businesses and over 25 manufacturing experts contributed to the roadmap. E-REP worked with TEConomy Partners—a consulting firm specializing in research, analysis and strategy for economic development—to develop the report.
Anticipated impacts from the roadmap’s execution include better-paying jobs with higher growth potential, the strength to weather economic challenges and the inspiration of future generations to reach their full capabilities.
“E-REP wanted to better understand how we can support the growth of [the manufacturing] sector and then the sustainability and cultivation of that sector,” Stock said. “We want to advance this cluster from the manufacturing perspective. But, ultimately, we don’t want to end up with something so aspirational that it’s not achievable.”
The regional state of manufacturing
The roadmap revealed manufacturing-related industries account for 21% of total private-sector employment in the Evansville area, compared to 6% nationally. The industries represent 41% of total economic activity in the region, compared to the 8% national average. From 2017 to 2021, regional manufacturing employment levels grew by 7.7%, compared to regional private sector growth of -2% and national analogous manufacturing cluster growth of 1%.
The report indicated that the strength of the region’s manufacturing sector is led by several highly specialized sectors and key anchor companies, as well as a diversity of products. The top five clusters of regional employment are motor vehicle manufacturing, polymers and plastic products, food processing and manufacturing, metals manufacturing and fabrication, and machinery manufacturing.
Despite pandemic-related disruptions to manufacturing industries worldwide and declines in overall private-sector employment in the Evansville region, the growth of local manufacturing jobs has persevered.
“The state of manufacturing [in the region] is strong … the sector is growing; it’s outpacing state and national averages from an economic standpoint. From the technology adoption standpoint, it’s doing well, but there’s room for improvement,” Stock said.
“Investing in automation has become a more significant trend in terms of the pace that it had been going in the last probably three to five years,” added Daniela Vidal, chancellor at Ivy Tech Community College in Evansville and member of the roadmap’s project steering committee. “That’s picked up quite a bit to respond to the labor shortages the manufacturing sector has been experiencing. That’s really helped accelerate new technologies and new skills that are needed.”
Scott Butrum, site digital lighthouse lead at AstraZeneca and member of the roadmap’s project steering committee, agreed with Stock and Vidal.
“The state of manufacturing in the region is good, but all the companies in the region will be able to make it great if we continue to work together,” he said.
Support digital change management and technology adoption
The roadmap’s first strategic effort—supporting digital change management and technology adoption—calls for developing an Industry 4.0 business process and digital change management roadmap for Evansville regional manufacturers. The plan is to use best practices from prominent companies, such as Toyota Indiana.
“The idea was to pull out a change management process for the region that small and medium-sized businesses could walk through and replicate in their operations and processes,” Stock said. “Helping them troubleshoot a step-by-step process for how they might go about determining whether they’re going to adopt a piece of technology within their operational production line.”
Other technology support recommendations include creating testbeds to de-risk the process of integrating new technology, connecting companies with technology funding opportunities and establishing a network of trusted evaluator-integrators.
“We want to feature on [E-REP’s] web page a list of integrators that are working with our manufacturing firms to help with technology adoption,” said Stock. “Then [we can] point other manufacturers back to that list if they don’t have an integrating partner they work with.”
Vidal pointed out that supporting technology adoption is not just about robots and automated production lines.
“There’s also a big component that often gets overlooked, which is your information and production management, [enterprise resource planning, material requirements planning] systems, which would also classify as part of smart manufacturing. Very expensive and difficult to implement,” she said.
“The point of the roadmap is to identify low-hanging fruit for employers to advance to Industry 3.0 and ultimately, hopefully, 4.0 and 5.0 when that happens,” added Stock.
Grow and align talent pipelines
The second roadmap strategy—growing and aligning talent pipelines—involves establishing training program hubs at educational providers in the Evansville region to develop specialized technical talent to address manufacturing industry demand.
“A lot of that is spending a lot of time with post-secondary advisory councils from their different educational departments and bringing our manufacturing partners into those spaces,” Stock said. “There’s some reality that engineers are graduating and not having some specific skills that our industry partners need, that our educational faculty don’t even realize they lack.”
Vidal said building a high-tech workforce that’s qualified for advanced manufacturing jobs is a complex issue.
“Businesses are not going to feel comfortable making that [technology] leap until they see they have the skills, the pipeline of workers. And it’s hard to build that pipeline of workers if [businesses] don’t have the jobs for them. We’re in that inflection point of needing both things to happen at the same time,” she said.
“Talent pipelines seem to be a common theme with the region, and we all have a lot of synergies to help grow this talent pool,” Butrum added.
Other talent pipeline actions include expanding K-12 exposure to manufacturing jobs and creating career ladders to attract entry-level workers.
“When you automate something, you move workers out of production and into maintenance reliability because now they’re working on a robot or a collaborative robot or a [programmable logic controller] rather than screwing in X widget to X plate,” said Stock. “A maintenance reliability person … what’s the career ladder for them? Potentially that career ladder could be continuous improvement manager, team lead, on and on and on.”
Vidal said Ivy Tech is creating new programs and strategies to help employers accelerate the upskilling and reskilling of existing employees.
“How do we look at that specific skill that [a worker] needs to operate that specific type of automation or specific program and give [them] those components as [they] need them, instead of having to commit two years or four years to do a whole program that may or may not completely fit with what that employer is needing at that moment,” she said.
Enhance ecosystem connectivity
The manufacturing roadmap’s third strategy—enhancing ecosystem connectivity—aims to fund a dedicated staff to coordinate outreach, partnership-building and matchmaking services to boost Industry 4.0 adoption in the Evansville region.
“When you think about talent pipelines and technology adoption, it all takes resources and collaboration,” said Stock. “What we can do is pull in all of our region’s different assets, so post-secondary partners, venture capitalists, state funding through the [Indiana Economic Development Corp.], and we can align those resources back to what our industry partners need.”
Other ecosystem connectivity actions include expanding peer networking groups across the manufacturing sector and pursuing broader resources.
“The idea is how do we bring content experts from outside manufacturing firms to places where innovation and best practices are happening, and then they can take that information and those insights back to their firm and continue to grow their institutional knowledge,” said Stock.
Stock said ecosystem connectivity is vital for digital change management, technology adoption and talent pipeline growth to occur in the region.
“It’s connecting [components] in a way that we can attract investments and say, ‘Here’s an area that’s a hub for next-generation automotive,’ because we have the advanced materials, the batteries, the electronic components and even the [original equipment manufacturers] like Toyota,” Vidal added. “We can build those networks and ecosystems, so we not only have the specialized workforce but also the supply chain within our region to support and grow it.”