Energy INsights program focuses on reducing energy costs for manufacturers
Subscriber Benefit
As a subscriber you can listen to articles at work, in the car, or while you work out. Subscribe Now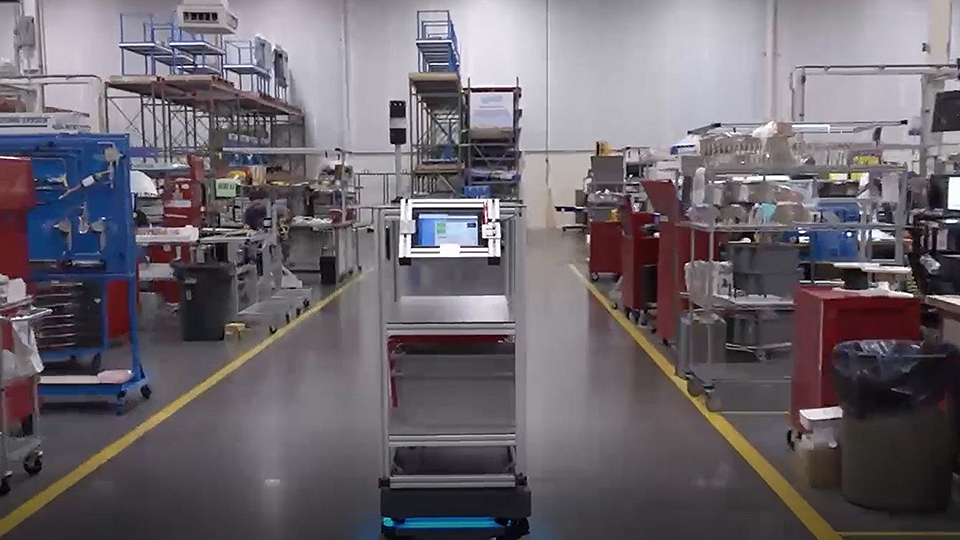
The president and CEO of Energy Systems Network in Indianapolis says a recently-launched program aims to help Hoosier manufacturers deal with increasing industrial energy costs. The state’s advanced energy technology initiative this spring announced the launch of Energy INsights, which seeks to use artificial intelligence and data science to not only reduce costs for manufacturers, but improve sustainability.
“When it comes to understanding their energy consumption and what they can do at an operational level with the actual machinery and equipment that are used in the manufacturing processes, that can be really challenging and expensive, historically,” said Paul Mitchell.
Mitchell says companies have been looking for ways to reduce energy consumption for years.
Mitchell says deploying new, emerging and cutting edge technologies can not only help with energy costs, but other operational efficiencies, such as cloud computing and data analytics.
“That whole concept has been something that the Indiana Economic Development Corp. and Energy Systems Network had been thinking about for a couple of years,” said Mitchell. “What was unique about this particular program is we found a world-class partner from industry that had the same goals as the state.”
ESN and the IEDC are partnering with Amazon Web Services (AWS) to deploy the Energy INsights program for at least 100 manufacturers throughout the state.
The partners say manufacturers will integrate the I4.0 Accelerator from AWS, which can gather data from their legacy factory equipment and energy management systems. The companies would then be able to use the data to optimize their energy efficiency with the goal of reducing energy costs up to 20%.
The program began as a pilot last fall with two Indiana companies: Amatrol Inc. in Jeffersonville and Fort Wayne Metals.
Mitchell says one of the biggest lessons that was learned was how to improve and speed up the deployment of the program without disrupting the company’s operations.
“The longer term learnings that will lead to significant energy savings and/or improved operational efficiencies, that will take some time to play out because you first have to begin collecting millions, even potentially trillions of data points from the machinery and from the facility, get it into the cloud and conduct machine learning, AI, data science to that data to generate meaningful insights that look at and look for anomalies, look at failure points to then say, ‘Hey, these are ways you can improve things,'” he said. “So it wasn’t like you switch it on and within minutes or hours or days or even weeks that you’re going to immediately start to see a 10 20% reduction in your energy consumption.”
He says the early pilots will help the installation of the technology at each manufacturer take hours rather than days to complete.
The program is also being done in conjunction with the Emerging Manufacturing Collaboration Center (EMC2) in Indianapolis, which will help with the installation of the technology and provide support.
Mitchell says the EMC2 facility at the 16 Tech Innovation District in Indy will serve as a “living lab” for the program.
“The technology that’s being deployed to these manufacturing sites has already been deployed there at that site. So people can go, they can see it, they can see the data, they can test it out. We also are doing trainings and workshops at that facility on the program for manufacturers, for utilities, for regional organizations who deal with manufacturers.”
Mitchell says the EMC2 will soon host “bring your machine to work days” where companies can specifically see how a particular machine can be optimized for operational efficiencies, predictive maintenance, and other energy efficiencies.
Looking forward, Mitchell says the program is already being developed to expand across the country and the world through AWS.