‘Invisible’ Digital Twins Taking Flight at GE Aviation
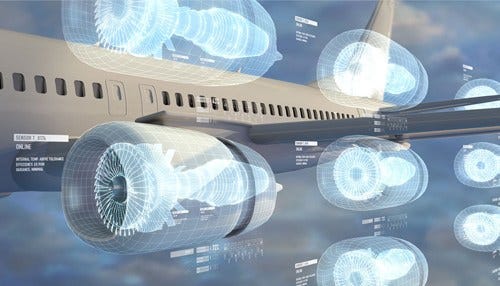
Subscriber Benefit
As a subscriber you can listen to articles at work, in the car, or while you work out. Subscribe NowAs aircraft engines roll off the production line at GE Aviation in Lafayette, workers there are also producing “ghost” engines of sorts, called digital twins. The cutting-edge digital replicas exist for each individual engine, giving the company an electronic trail for every single one—allowing GE to monitor its performance, predict maintenance issues and, ultimately, reduce costs long after the engine leaves the plant.
While digital twins are gaining traction in many industries, GE Aviation says it’s one of the companies leading the technology’s adoption. Eric Matteson is the executive plant leader at GE Aviation’s Lafayette Engine Facility, which opened in 2015 and builds engines for Airbus’ A320neo, Boeing’s 737 MAX and Comac’s 919—all recognizable planes to the average airline passenger. On each engine that rolls off the line in Lafayette, he says there are about 2,000 critical characteristics that will help determine its performance.
“We capture data on each of those characteristics as we put the engine together,” says Matteson. “It’s a massive amount of data; a flight to Europe, for example, is about half a terabyte per engine.”
With two engines per plane, that’s enough data to fill a computer’s entire hard drive. Every single flight, the information is collected electronically via sensors on the engine that are connected to the engine control unit. That mind-boggling amount of data is gathered, organized and transmitted to the digital twin, so it’s always up-to-date with the actual engine in the field.
“We gather data from each flight while it’s flying or once it pulls up to gate. We download data from the flight data management system, the weather satellites and so forth,” says Matteson. “With this digital replica of the engine, we can use predictive analysis to model where it’s going to need service and what kind of service it’s going to need as that engine ages. Then, we can optimize the turnaround time to get it back to wing sooner, returning more flying days for that engine per year.”
Matteson says GE has been collecting massive amounts of engine data for about 15 years, but the recent emergence of the Internet of Things (IoT) makes the information come to life.
“There was a massive amount of data that we were collecting [about 15 years ago] that we just never analyzed because it was hard—it was in different databases and not easy to use,” says Matteson. “What’s changed now is the data is freely going into databases, and we have superior computing power to convert that data to metadata, do predictive analysis on it and provide that information to humans who can make smarter decisions faster.”
Digital twins are accessible throughout GE’s facilities, including the Lafayette operation, where Matteson says the technology is especially helpful for the maintenance, repair and overhaul team.
“For a customer like an airline, the vast amount of data that comes off the engine isn’t as interesting to them as when we can tell them, ‘You’re going to have to take the engine off at this date,’” says Matteson. “Now we can plan together, so it doesn’t impact that aircraft’s service. We’re maximizing the total value proposition of the aircraft and equipment.”
Of the 65,000 installed GE engines, the manufacturer is collecting data on about 35,000. Analysts can look at a single digital twin or combine many to produce a big-picture perspective of an entire fleet.
Every engine produced at the Lafayette plant—currently, about eight per week—has a full digital twin. Matteson says the concept is being applied across many industries; GE is working to increase its use on locomotives and healthcare equipment, for example.
Unbeknownst to the typical airline passenger, Matteson says digital twins are constantly churning in the background of every single flight, with GE crunching data—a tool that Hoosier workers are building into each Indiana-made engine to help a new technology take flight.
Matteson says, on its most basic level, a digital twin “connects real-time information to people,” much like some smartphone apps.
Matteson says an emerging use of digital twins is analyzing data to look at factors like fuel burn—saving the customer even more money.